デジタル印刷機の存在感が増すにつれ効率的なワークフローの構築が求められつつある。オフセット印刷と同様の生産管理では大量のジョブを効率的にコントロールするのは難しい。
そこで重要になると考えているのが製造実行システム(MES:Manufacturing Execution System) という概念である。
もともとは2011年に掲載した記事であるが再掲する。 PAGE2011カンファレンスでの(株)メタテクノ山野俊彦氏のお話を中心にMESの考え方をまとめたものである。
標準印刷色など各種標準化の取組みは進みつつあるが、個別受注生産かつ校正という不確定要素の高い工程を持つ印刷業では、ワークフローの標準化や効率化は依然として大きな課題である。工程の自動化を可能とする電子的なジョブチケットの代わりに印刷物の現物見本と注意点や変更点が書き込まれた紙の作業指示書が工場内を流れ、品質の安定化や効率的な生産は、現場の人の技量と経験と知恵に頼る部分がまだまだ大きい。人手に頼った効率化には限界がある一方で、現場を支援するシステムも複雑な工程で多品種少量の生産を行うワークフローをマネジメントしきれないという現状がある。
印刷業で使われている業務システム(MIS)の多くは、販売管理システムから発展したもので経営情報データベースシステムという位置づけで、きめ細かな生産管理は得意としていないように見受けられる。
というのも、業務システムは受注から納品までの顧客対応を主眼に製品情報や売買情報をトラッキングするためのものであり、扱う情報の時間軸は月・週・日という単位が中心である。
見積りが了承され受注が確定すると、製造設計・日程計画を作成し各工程に対して指示情報が流される。この指示情報を工程の最後まで、そのままの形で流すことができるとよいのだが実際にはそういかない。得意先の都合、あるいは自社の現場の状況により何度も変更を余儀なくされる。
生産管理で求められるのは指示に基づいた作業結果を適切かつタイムリーに判断し、その結果によって次工程以後の作業にゴーサインを出したり、時には工程や順番を入れ替えたり内容を変更したりすることである。ここで扱う情報は動的なものであり、その時間軸は時・分・秒という単位である(図)。
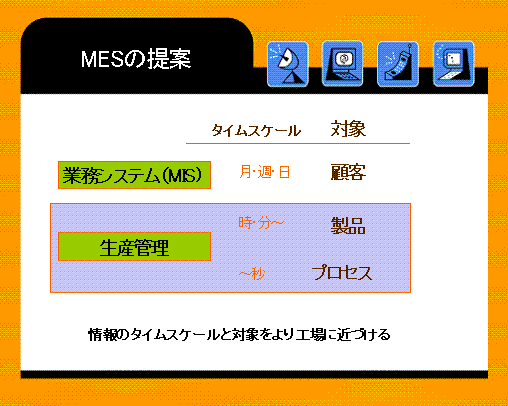
業務システムの時間軸と生産管理で求められる時間軸の差を埋める仕組みをうまく構築できないために、「ウチのシステムは融通が利かなくて使えない」という評価になってしまうと考えられる。さらに工程の自動化や生産機器の自動プリセットなど、より高度な処理を行おうとするならば、静的な受注情報だけでは不足が生じる。特に前工程の処理結果を受けて次工程の設定をする必要があるような場合、圧倒的な情報不足に陥る。日本においてJDFワークフローの普及がなかなか進まない大きな要因と考えられる。
こうした課題を解決するための提案が、業務システムですべてを賄うのではなく生産管理の機能を分離するというものである。プロセス産業と呼ばれる製造工程の複雑な製造業(例:石油精製、化学、食品、医薬品など)では、“生産実行システム(MES:Manufacturing Execution System)”と呼ばれるシステムの導入が1990年代後半から進んでいる。業界によってシステムの形態はさまざまであるが、業務システムとの役割分担を端的に表現すると「何を作るか」「何を作ったか」を業務システムが管轄し、「どのように作るか」「どのように作られたか」を生産実行システム(MES)が管轄することになる。この概念を印刷業に取り入れることで、より柔軟で拡張性の高い生産管理、ワークフローシステムが構築できるようになると考えている(図)。
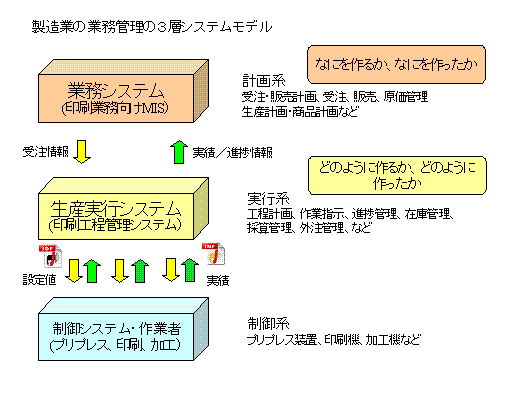
MISから「何を作るか」の指示をMESに対して出す。それを受けてMESが「どのように作るか」という指示を設備の制御システムや作業者に対して適宜出していく。生成される情報は静的な情報から動的な流れを管理する情報に変わることになる。
それぞれの工場の設備や求められるワークフローに応じて、工程は設備や人的作業も含めて入力と出力が明確化され、すべての工程の出力は次の工程のパラメーターとして活かされるようになる。
このようにして従来の作業指示書レベルでは表現されない作業結果情報を動的に次の工程へと確実にスピーディーに渡していく環境を整えたうえで、情報交換の標準フォーマットとしてJDFを活用することにより全工程の最適化が実現されて行くと考える(図)。
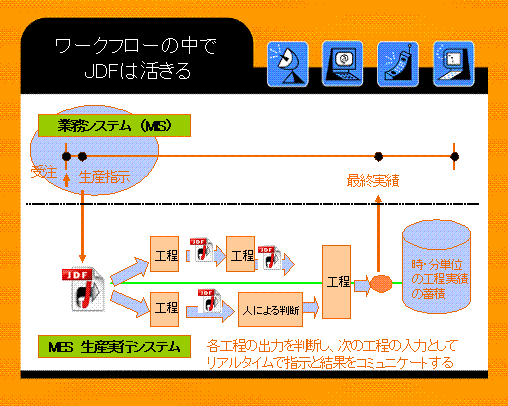
JDFの利用に限らず、こうした工程管理システムとプロセス制御の手法は、各工程それぞれの自動化・効率化を推し進めるだけでなく、それぞれの結果を意味ある情報として次の工程に結びつけるもの、また、単に2つの工程を結ぶのではなく、出力に対する条件判断を行えるようにし、次に何をすべきかという工程分岐の自動化・効率化にも寄与すると考えている。
さらには、生産指示から作業完了までに発生するさまざまなコミュニケーション・情報交換をIT支援で活性化し、見える化し、個人的な経験則を社内の共有財産、ナレッジとすることが可能になるはずである。
(研究調査部 花房 賢)